Research
- Remote measurement of adhesion in piping by scanning laser source technique
- Spatial visualization by ultrasound in poor visibility and high radiation conditions
- In-process defect inspection of additive manufacturing products
- Development of buffer for ultrasonic phased array using waveguides
- Application of laser ultrasonics in Cryo Ultrasonic Testing
- Nondestructive characterization for adhesive joints/coating layers by ultrasonic spectral analysis
- Fundamental and application studies of local resonance phenomena in thin layers and thin-walled components
- Monitoring for curing adhesives and resins and adhesion reinforcement using ultrasonic waves
- Analysis of Organic Field-Effect Transistors
- Evaluation of Mechanical Properties of Magnesium Alloys
- Integration of Machine Learning and High-Performance Computing
1. Remote measurement of adhesion in piping by scanning laser source technique
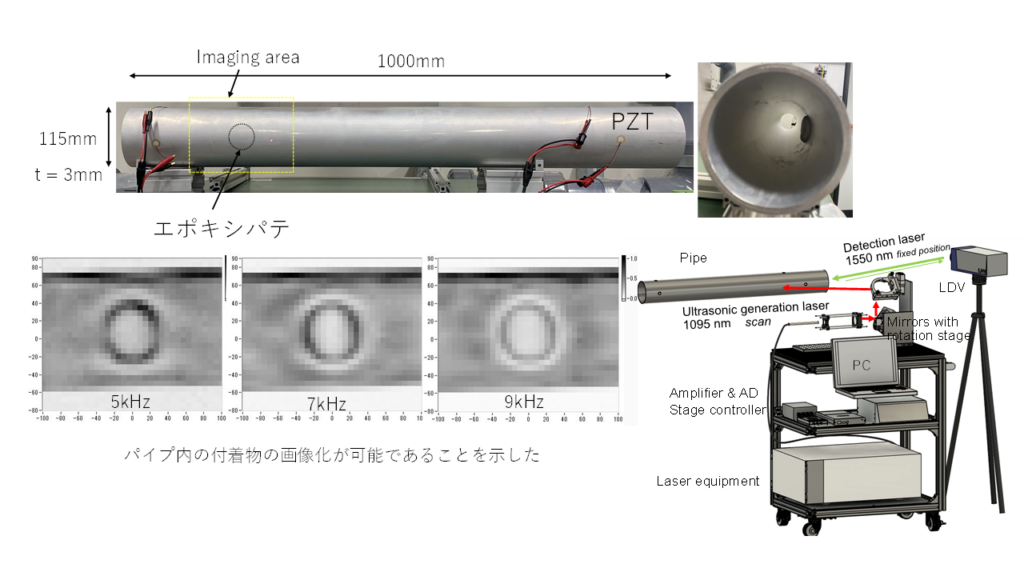
Laser Ultrasonics, in which ultrasonic waves are generated in a solid material by a laser and the vibrations propagated through the solid material to the surface are detected by another laser, has been used for nondestructive inspection and material evaluation. Our group is studying the scanning laser source technique to apply Laser Ultrasonics for diagnostics of large structures, especially for piping inspections.
As a part of the application development, we aim to apply this method to remote measurement of deposits in piping for decommissioning of nuclear power plants. The figure above shows imaging results of an artificial adhesion in a pipe measured from a distance of 3.5 meters. The results show that an image of the adhesion can be obtained when the adhesion is on the laser irradiated side.
This work is supported by JAEA Nuclear Energy S&T and Human Resource Development Project through concentrating wisdom Grant Number JPJA23P23813810.
Main contact: Takahiro Hayashi
2. Spatial visualization by ultrasound in poor visibility and high radiation conditions
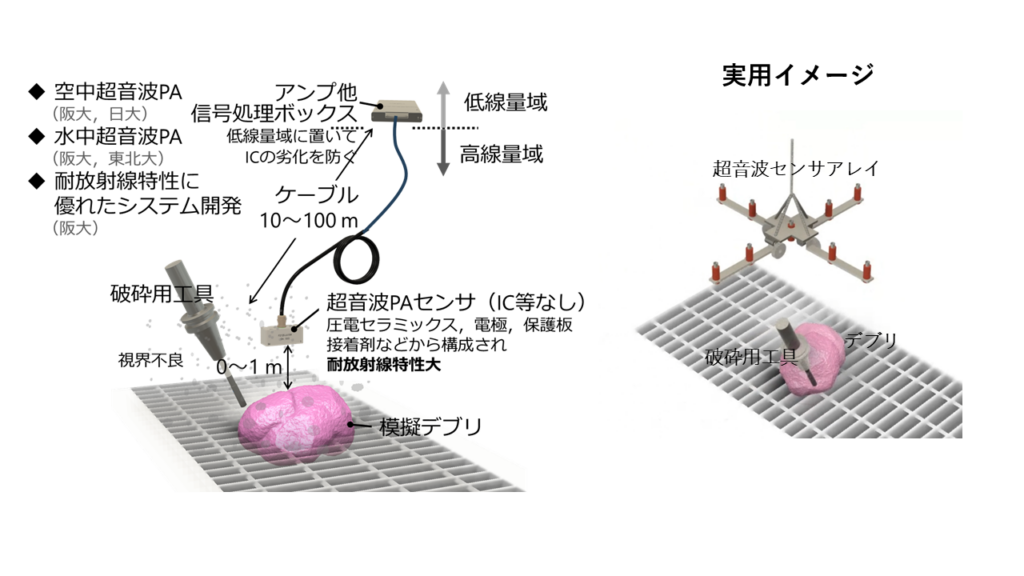
Fuel debris removal is one of the most important tasks in the decommissioning of the Fukushima Daiichi Nuclear Power Plant. During the debris removal, optical and infrared cameras often cannot see the debris, tools, and surrounding environment due to poor visibility caused by dust and suspended particles. In addition, these cameras do not work properly near radioactive materials and may break down.
In this study, we are investigating ultrasonic phased array technology as a new visualization technique for spatial recognition. The wavelength in the low frequency band (20 kHz to 1 MHz) is sufficiently small compared to the size of dust and suspended particles, and ultrasonic waves diffract to reach objects, so phased array technology can be used without problems. Furthermore, the ultrasonic sensor is composed of piezoelectric ceramic and passive elements and does not contain any semiconductor chips, making it resistant to radiation. Therefore, by bringing the ultrasonic phased-array probe close (e.g., 1 m) to the point where spatial recognition is required and placing the measurement device part including semiconductors such as amplifiers and AD converters away from the radioactive material, visualization technology in difficult environments such as poor visibility and high radiation levels will become possible. This research is being carried out in collaboration with Tohoku University, Nihon University, and Department of Environmental Energy Engineering, Osaka University.
This work is supported by JAEA Nuclear Energy S&T and Human Resource Development Project through concentrating wisdom Grant Number JPJA24P2420343.
Main contact: Takahiro Hayashi
3. In-process defect inspection of additive manufacturing products
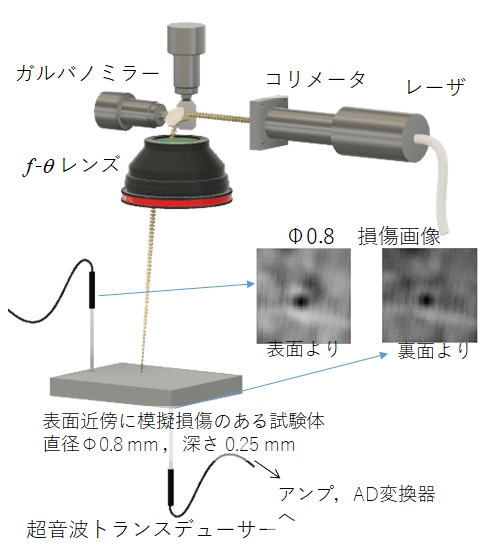
In additive manufacturing process of metal power bed fusion, 3D printers create 3D shapes by repeatedly sintering and melting thin layers of metal powder and solidifying only the modeling area. This process makes it possible to fabricate parts with shapes that cannot be realized with conventional machining process. However, micro defects are often generated due to voids and inadequate melting, causing a reduction in the strength of the modeled part. In addition, completed moldings are often complex in shape, making post-processing inspection difficult. Defects that appear on the surface of the object can be detected by camera images, but many defects are buried near the surface layer, making the detection of such defects a challenge.
Our research group has developed a technology that enables non-contact imaging of microdefects near the surface layer using ultrasonic waves generated by laser irradiation, and has completed a basic technology that enables inspection while molding. This technology has been released in press.
Main contact: Takahiro Hayash
5. Development of buffer for ultrasonic phased array using waveguides
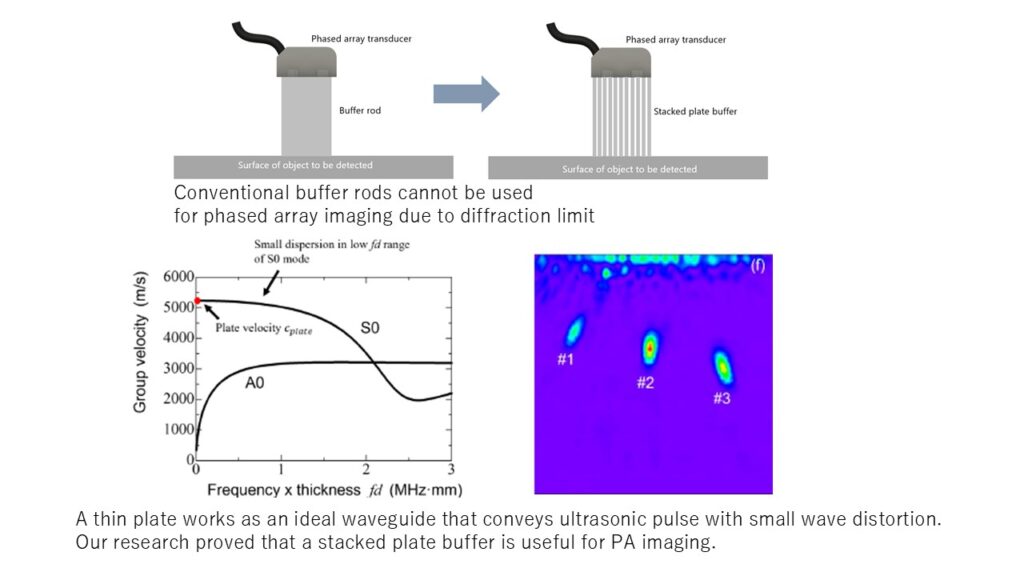
Ultrasonic phased array technology is being used everywhere. This technique processes ultrasonic waveforms output from and received by a number of elements to obtain images of reflective objects inside materials such as defects and interfaces. In general, the ultrasonic phased array probe is in contact with the object, making it difficult to apply the technique to hot objects such as in-service piping. When inspecting such high-temperature objects, a buffer rod is inserted between the ultrasonic probe and the object to reduce the temperature rise of the probe while the ultrasonic waves are incident into the object. However, wave theory has proven that the combination of ultrasonic phased array technology and buffer rod does not provide an image of the interior of the object.
We have developed an ultrasonic phased array with a thin plate wave guide attached to each vibrating element, which enables us to image internal defects with a buffer attached as if the ultrasonic phased array probe were actually present at the exit of the waveguides.
Main contact: Takahiro Hayashi
5. Application of laser ultrasonics in Cryo Ultrasonic Testing
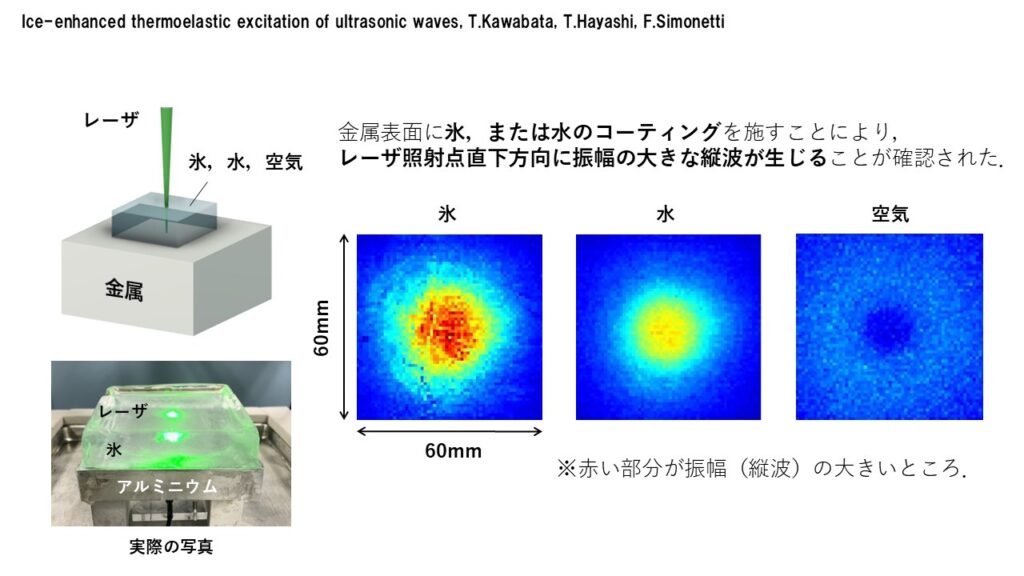
For metal complex parts produced by additive manufacturing, inspection by the ultrasonic water immersion method is currently difficult due to various factors. The first factor is that the surface of the material is not flat, making it difficult to image by C-scan, which is often used in the water immersion method; the second factor is that it is difficult for ultrasonic waves to penetrate into the material due to the large difference in acoustic impedance between the water and the metal material, and the critical angle of the ultrasonic waves prevents energy transfer to the slope.
To overcome these challenges, Prof. Francesco Simonetti’s group at the University of Cincinnati has established the Cryo Ultrasonic Testing, which can detect defects in slopes and complex structures by freezing water to increase its acoustic impedance and transmitting and receiving ultrasonic waves from the ice surface using a phased-array probe.
In collaboration with the Univ. of Cincinnati, our group has been experimenting with Laser Cryo-UT technology, which combines Cryo-UT with laser ultrasonics. When air, water, and ice are on the surface of a metallic material, the surface is irradiated with pulsed laser pulses and excited with ultrasonic waves, each of which exhibits a unique ultrasonic propagation pattern.
Main contact: Takahiro Hayashi
6. Nondestructive characterization for adhesive joints/coating layers by ultrasonic spectral analysis
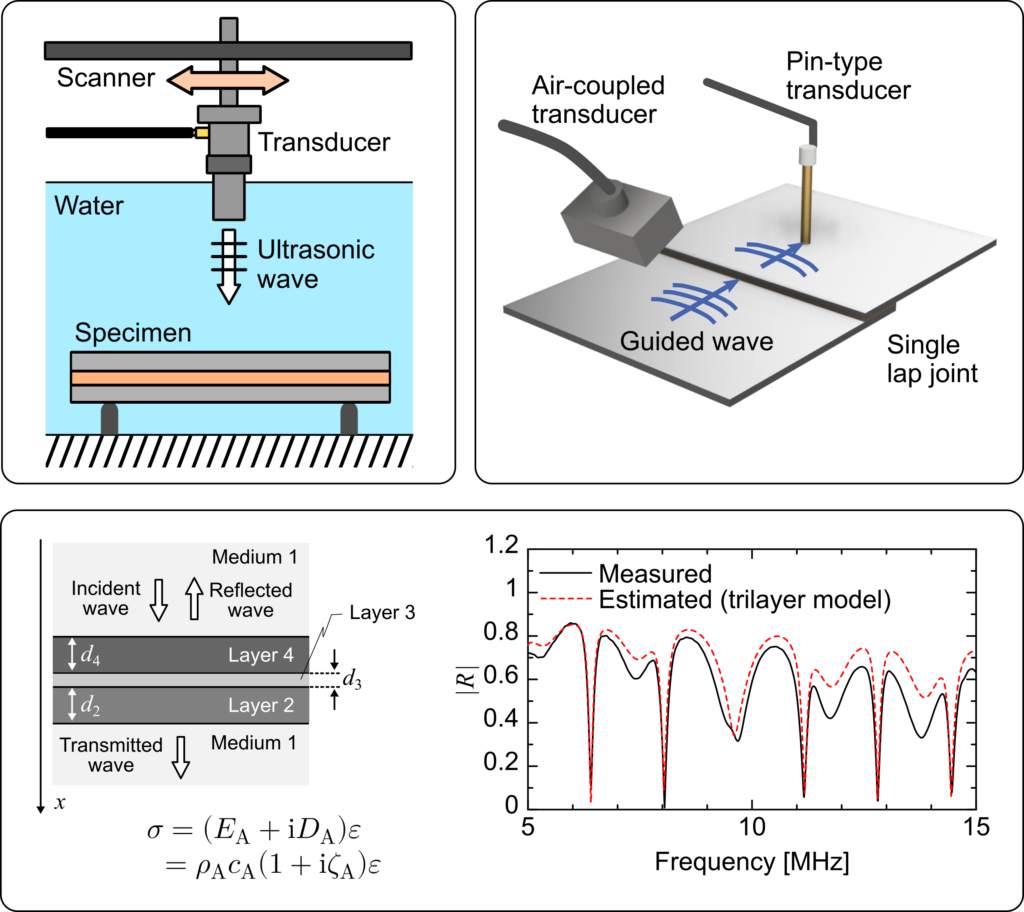
In recent years, adhesive bonding has attracted attention due to its advantages compared to mechanical fastening, such as weight reduction and stress concentration relaxation. The application of adhesive bonding is growing in structures with various scales and purposes, such as automobiles and devices, as well as traditional usages like aircraft.
One of the challenges in adhesive bonding is the characteristic variation of cured bonded joints. Expanding its application further requires nondestructive characterization techniques for adhesive joints. This project aims to develop quantitative evaluation methods for the properties of adhesive/coating layers, as well as interfaces, based on interference/resonance phenomena for ultrasonic wave incidence.
Main contact : Naoki Mori
Journal Paper
- N. Mori, N. Matsuda, T. Kusaka, “Effect of interfacial adhesion on the ultrasonic interaction with adhesive joints: a theoretical study using spring-type interfaces,” Journal of the Acoustical Society of America, 145 (6), 3541–3550, 2019. https://doi.org/10.1121/1.5111856
- N. Mori, D. Wakabayashi, T. Hayashi, “Tangential bond stiffness evaluation of adhesive lap joints by spectral interference of the low-frequency A0 Lamb wave,” International Journal of Adhesion and Adhesives, 113, 103071, 2022. https://doi.org/10.1016/j.ijadhadh.2021.103071
- N. Mori, Y. Iwata, T. Hayashi, N. Matsuda, “Viscoelastic wave propagation and resonance in a metal-plastic bonded laminate,” Mechanics of Advanced Materials and Structures, 30 (18), 3803–3816, 2023. https://doi.org/10.1080/15376494.2022.2084191
7. Fundamental and application studies of local resonance phenomena in thin layers and thin-walled components
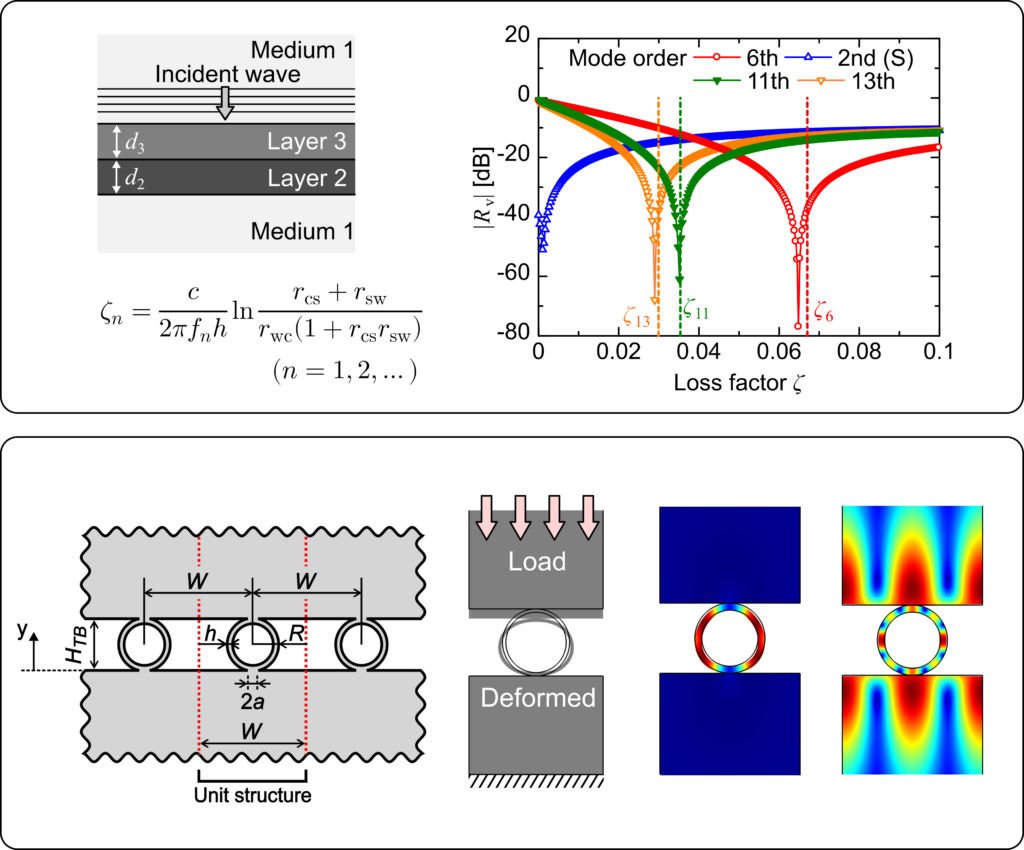
Understanding elastic wave propagation behavior in solids is essential to design structures and devices for controlling sound and vibrations, such as sound absorbers and acoustic wave filters. If a structure has a locally low stiffness part, local resonance can sometimes occur at vibration frequencies associated with the wavelength of elastic waves. This phenomenon can be applied to elastic wave amplification/suppression and steering in specific frequency ranges.
In this study, fundamental experiments and numerical analysis are performed for local resonance phenomena appearing in thin-walled parts, aiming to their applications to ultrasonic nondestructive evaluation and active tuning for elastic wave propagation.
Main Contact: Naoki Mori
Journal Paper
- N. Mori, T. Hayashi, “Ultrasonic interference and critical attenuation in metal-plastic bilayer laminates,” Journal of Sound and Vibration, 547, 117531, 2023. https://doi.org/10.1016/j.jsv.2022.117531
- A. Sasaki, N. Mori, T. Hayashi, “Tunable elastic wave transmission and resonance in a periodically aligned tube-block structure,” Journal of the Acoustical Society of America, 156 (1), 44–54, 2024 https://doi.org/10.1121/10.0026462
8. Monitoring for curing adhesives and resins and adhesion reinforcement using ultrasonic waves
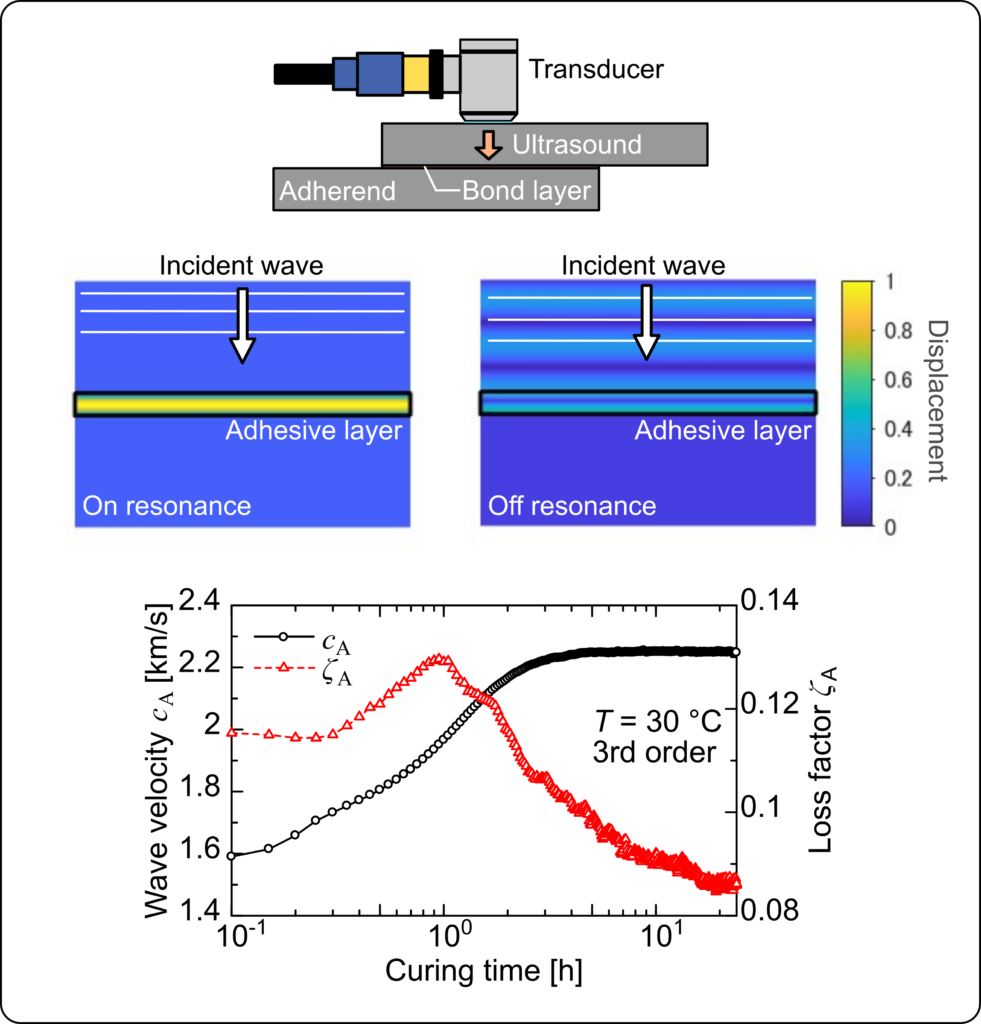
Adhesive joining utilizes bonding forces arising from various interactions, such as anchor effect, intermolecular forces, and chemical bonding. However, some of their processes and mechanisms are still open issues. This study aims to build ultrasonic monitoring methods for the viscoelastic properties of curing resins. Since ultrasonic waves can propagate inside solids, they are also applicable to composite structures like adhesive joints.
Furthermore, we conduct research regarding layer resonance-assisted adhesive bonding based on the resonance phenomenon of adhesive layers.
Main contact: Naoki Mori
Journal Paper
- N. Mori, T. Hakkaku, T. Hayashi, “Curing monitoring of adhesive layers between metal adherends by ultrasonic resonance technique,” Measurement Science and Technology, 36, 015605, 2025. https://doi.org/10.1088/1361-6501/ad8f51
9. Analysis of Organic Field-Effect Transistors
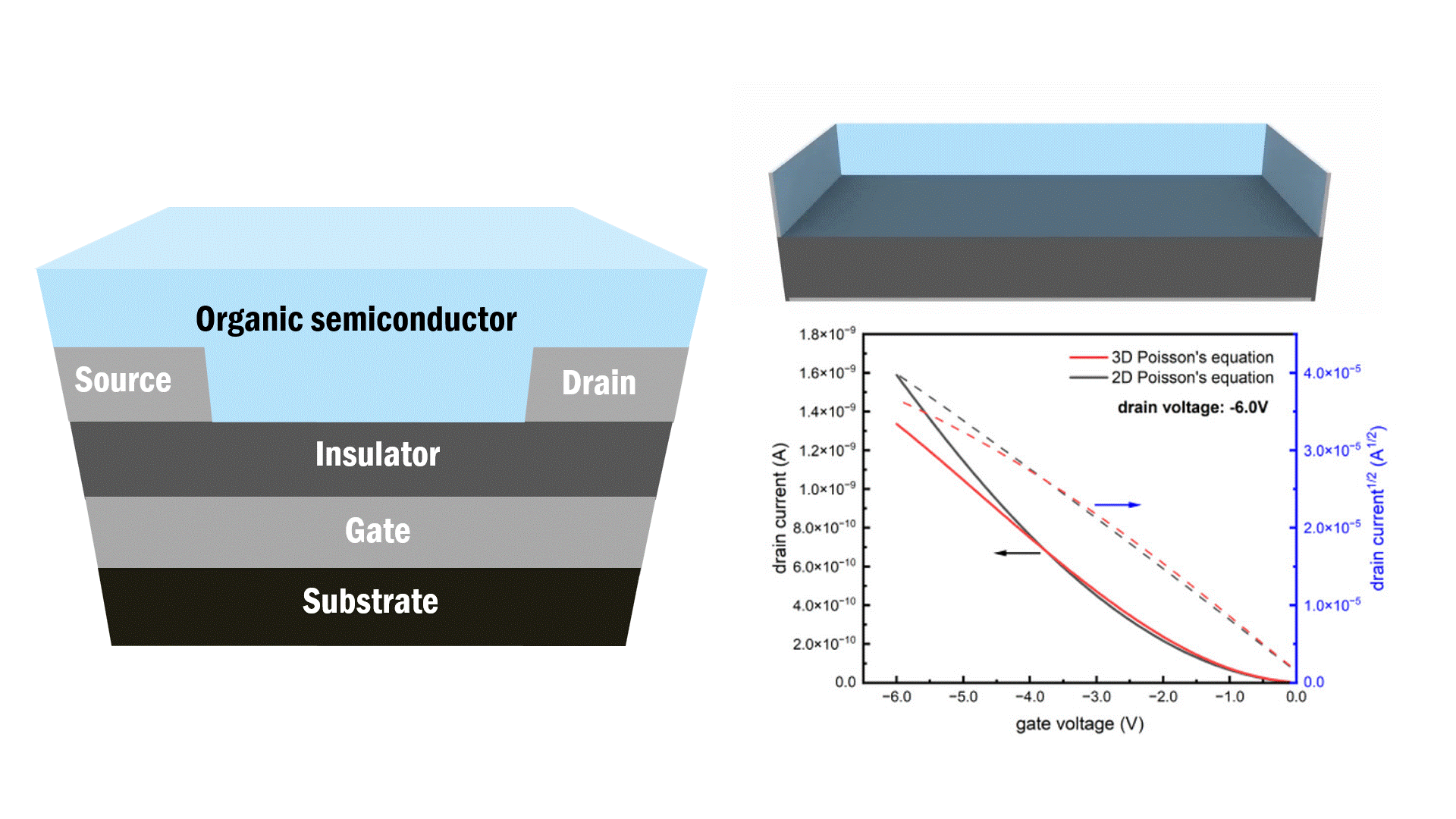
The Organic Field-Effect Transistor (OFET) is recognized as a pivotal device in applications such as flexible circuits, sensors, and memory storage. However, its performance typically lags behind that of inorganic counterparts. Enhancing the performance of OFETs necessitates precise control over the characteristics of the organic semiconductor layer.
Recent advancements in molecular-level simulation techniques, including kinetic Monte Carlo methods, have significantly enhanced the capability to replicate the microscopic behavior of charge carriers. Nevertheless, these approaches often depend on two-dimensional Poisson equations, which inadequately capture short-range electrostatic interactions.
In this research, we successfully employed a three-dimensional partial differential equation solver to model OFET devices, fully accounting for the Coulomb interactions between charge carriers. Our findings reveal that at elevated gate voltages, the transfer characteristics derived from the three-dimensional Poisson equation exhibit a downward curvature and lower values compared to those predicted by two-dimensional Poisson equations, suggesting strong concordance with experimental observations.
Main contact: Lijun Liu
Journal Paper
- Adv. Theory Simul. 2024, 2301259. https://doi.org/10.1002/adts.202301259
10. Evaluation of Mechanical Properties of Magnesium Alloys
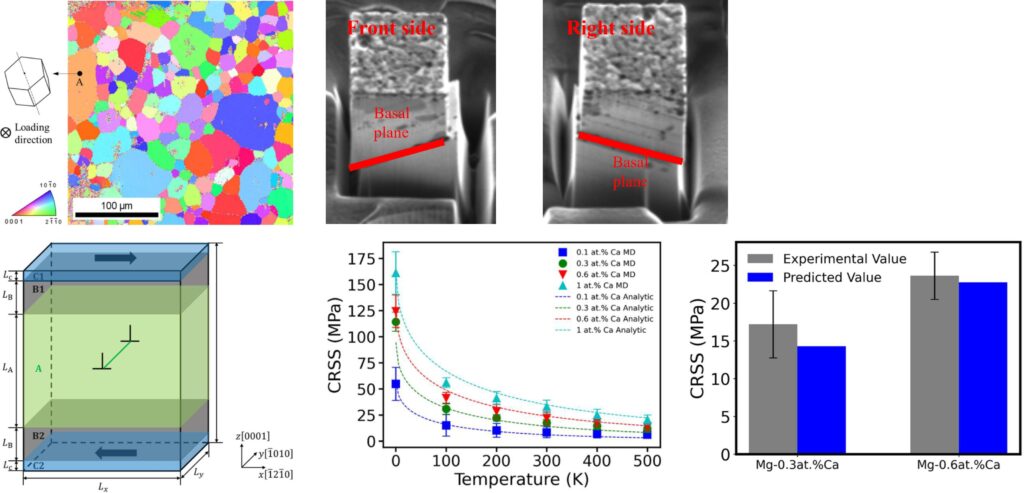
Magnesium (Mg) is recognized as the lightest structural metal and serves as a promising alternative to heavier steels and aluminum alloys. Nevertheless, Mg exhibits limited plastic formability at room temperature and generally displays inferior strength compared to most aluminum alloys. This constraint in formability can be attributed to the significant disparity in critical resolved shear stress (CRSS) between basal slip systems and other slip and twinning systems. Consequently, the low CRSS acts as a limiting factor for the strength of Mg alloys, underscoring the importance of enhancing basal slip to improve their strength, deformability, and fracture toughness.
This study presents a theoretical model aimed at predicting the CRSS in single-crystal Mg–Ca alloys. We quantitatively investigated the CRSS of basal dislocation slip along the basal plane using molecular dynamics simulations across a temperature range of 1 K to 500 K. The results obtained from the proposed theoretical model agree well with both simulation findings and micro-pillar compression test results for Mg–0.3 at.% Ca and Mg–0.6 at.% Ca alloys at ambient temperature.
Main contact: Lijun Liu
Journal Paper
- Materialia 32 (2023) 101900. https://doi.org/10.1016/j.mtla.2023.101900
11. Integration of Machine Learning and High-Performance Computing
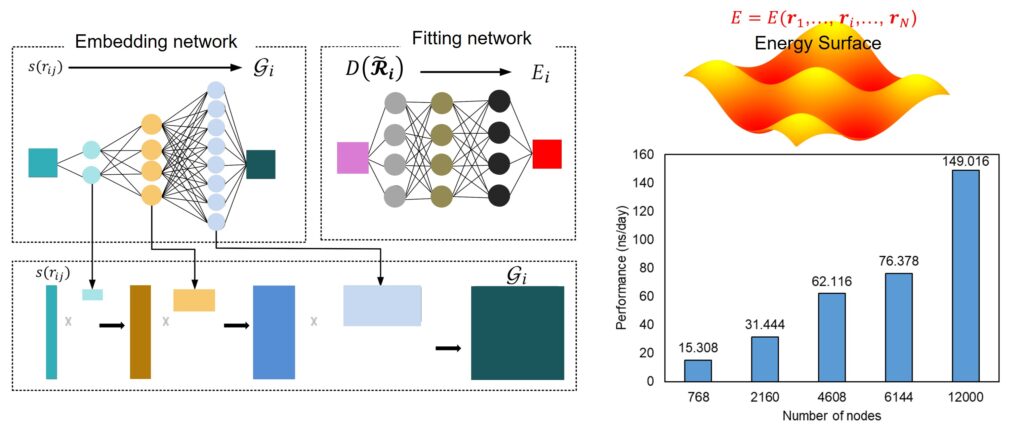
The optimization of material structures and the design of new materials rely on accurate property predictions through high-precision computational methods. While conventional macroscale modeling addresses real-scale simulations, it often depends on empirical approaches that limit accuracy. Conversely, atomistic-level techniques like ab initio molecular dynamics (AIMD) offer high precision but come with high computational costs, restricting the time and spatial scales that can be simulated. As chemical reactions and phase transitions occur on millisecond to microsecond time scales, reproducing these phenomena with AIMD is challenging, highlighting the need for rapid, high-precision analytical methods.
In this study, we employed a machine learning-based interatomic potential model for optimization on the Fugaku supercomputer, maintaining the accuracy of potential energy and interatomic forces. This approach resulted in a 31.7-fold increase in the computational speed of molecular dynamics (MD) simulations, achieving 149 nanoseconds per day across 12,000 nodes while retaining ab initio calculation accuracy.
Main contact: Lijun Liu
Journal Paper
- Proceedings of the International Conference for High Performance Computing, Networking, Storage, and Analysis (SC ’24). IEEE Press, Article 30, 1–15. https://doi.org/10.1109/SC41406.2024.00036